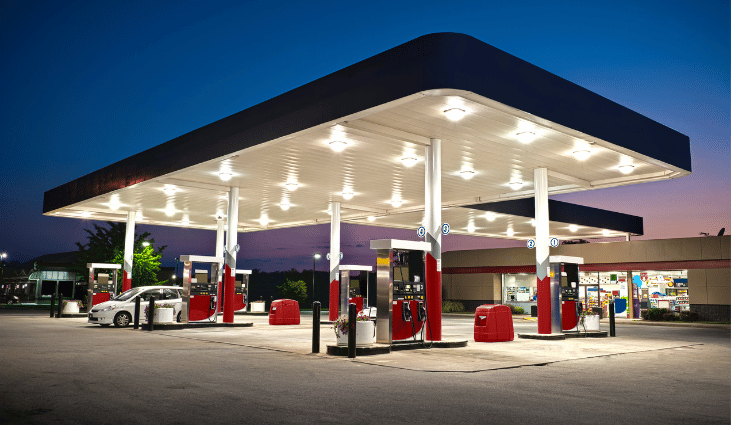
Fuel Inventory Variance Part 2: The Significance of Fine Grain Tank Charts
In the first two posts of this series, we discussed the domino effect of inventory variance across the fuel supply chain, and the vital role of fine grain tank chart technology in using high-frequency data capture to mitigate variance with pinpoint accuracy.
By now we know that managing fuel inventory variance is vital for operators looking to avoid lost product and revenue. More than simply the cost of doing business, these deficits can add up to big money in the wider picture.
Inventory variance is a multi-departmental responsibility, and response to issues usually depends on which operational functions are impacted. Stakeholders have differing perspectives based on their own concerns and budgets and tend to view matters from a more reactive viewpoint.
In the broader corporate sense, fuel businesses assume a certain amount of inventory variance, and typically respond only when a pre-determined threshold has been crossed. At that point, traditionally, a protocol is triggered. Companies may send out a team to investigate, often made up of specialists focused on the impacted area. An environmental team would address any compliance implications, for example, or a facilities team could be engaged to identify and plan remediation for maintenance issues.
All these approaches require time and money—potentially a significant amount, depending on what’s discovered during an investigation. In addition, investigations can further impact fueling operations by limiting customers’ ability to fuel while tests are being performed. All factors considered, 1% can add up to a considerable loss. Operators who proactively engage solutions to prevent such a domino effect, however, stand to increase revenue significantly:
Write-offs may be a given in most industries, but they don’t have to be a necessary evil; in fact, they can be greatly reduced to lessen the hinderance to business growth. Write-offs represent both a financial loss and an opportunity loss when budgets are shifted away from business enhancements to cover operational deficits.
So how do fuel operators get ahead of these losses? When a single digit threshold extrapolates to a revenue loss in the millions of dollars, even quick response to inventory variance issues isn’t good enough. Pinpointing variance factors in near real-time saves operational budget, which connects to revenue margins. Today’s fuel operators need to understand the bigger picture and take a more holistic approach to preventing fuel inventory variance altogether.
Inventory variance is a business problem regardless of industry; just ask any company accountant or corporate controller. At the C-level, executives see the more far-reaching implications of a compromised revenue cycle. This is particularly true in the extremely competitive retail fuel industry where operators can be fighting off stiff competition or positioning for merger activity on any given day.
The best way financial leaders in the fuel business can support getting ahead of inventory variance is to budget for investment in industry-specific, integrated technology that monitors systems and flags potential issues to pinpoint trouble spots in real time. Allocating funds to bring in this type of technical innovation now can save millions of dollars in the long run.
Global c-store leader 7-Eleven is a great example of this. The chain enlisted Titan Cloud’s help in automating operations, to detect and resolve inventory variance issues quickly. As a result, the company reported improved detection and mitigation of fuel loss and more efficient response to variance issues. Other Titan Cloud customers have recorded a lessening of inventory variance by up to 99%, with a 57% reduction in investigation costs.
By using connective data-capture technology like the Titan Cloud platform, operators can get answers to vital questions, be better positioned to fine tune the cause of variance and make informed decisions around where to put time and money. Key questions include:
In short, operators can use data generated by automated technology to understand the big picture, consider its interconnectivity, and take a more holistic approach to making better business decisions.
To learn how Titan Cloud’s end-to-end solution can help you detect and mitigate issues in near real-time and minimize write-offs, talk to one of our solution consultants here.