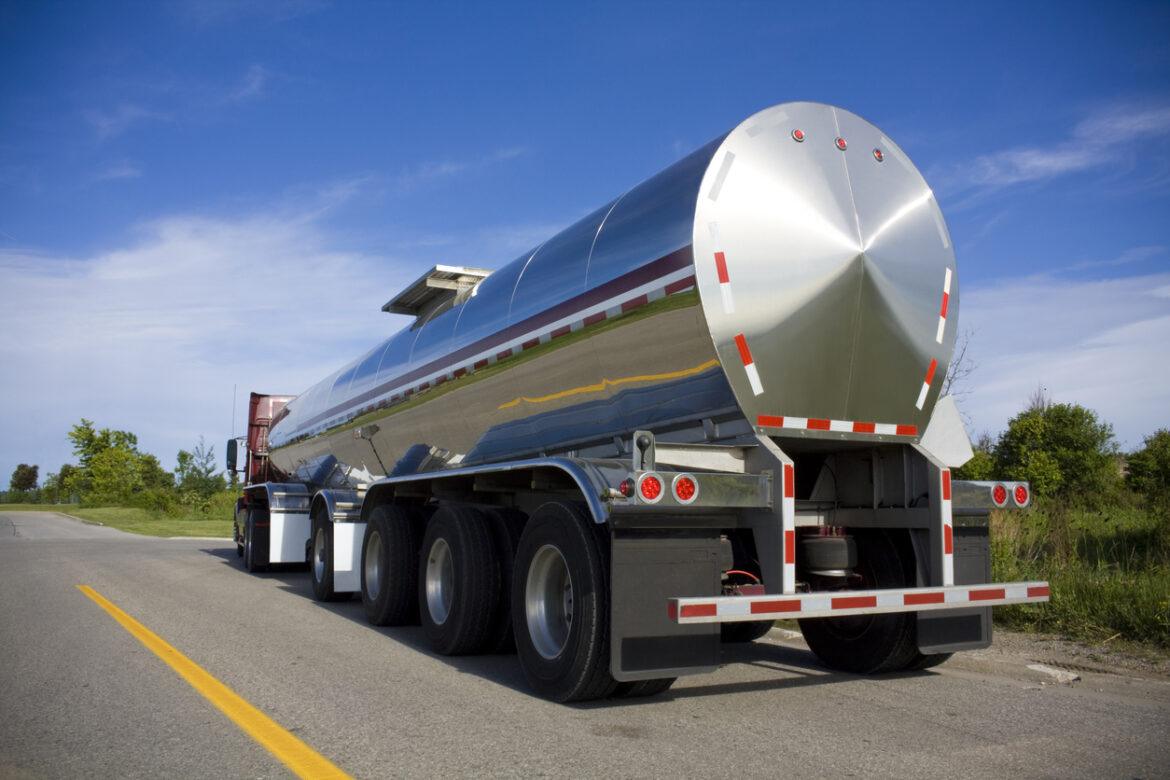
Supply Chain Logistics Part 1: Fuel Procurement, Contracts & Allocation
Welcome to the first in our 3-part blog series on fuel inventory variance, an often-silent culprit that can wreak havoc across the entire fuel supply chain from terminal to pump, resulting in significant revenue loss over time. Take the following example. Scale these numbers over multiple c-store locations and you’re easily looking at six-figure revenue losses.
In addition to financial implications, fuel variance is also an efficiency drain for fuel retailers. The time and effort needed to investigate discrepancies often lead to extended downtime and diverted resources. When issues go undetected, problems grow, multiple points along the supply chain are impacted, and resolution becomes costly. Staff members are taken off value-added work and operational costs increase. From the local retailer putting time into testing and troubleshooting, to the company controllers managing write-offs, the ripples are felt.
Throughout this series, we’ll explore how fuel variance presents at different stages of the fuel supply chain, and how its specific impacts are felt throughout the journey. We’ll discuss how today’s data-driven tank chart innovation can track and flag variance issues from terminal to pump to enable quick resolution before small issues become major losses. Finally, we’ll delve into the bigger financials to reveal the connection between proactively tracking inventory variance and avoiding unnecessary write-offs.
At the outset of the retail fuel supply chain, terminals and loading racks play a pivotal role. Here, fuel variance can emerge due to several factors, including temperature differentials that cause expansion or contraction of fuel volumes, leading to inaccuracies in inventory calculations. Terminal level calibration is also a factor, adding potential variance into the Bill of Lading (BOL).
Calculation and measurement errors at the start of the fuel supply chain can also mean starting the process behind the eight ball by paying too much to a supplier without getting the promised quantity. Not only do you pay more for less fuel upfront, but these errors snowball through the process. Inaccurate initial measurements can lead to inefficient deliveries, error-filled order histories, potential shortages, and ultimately wasted resources and costs.
It’s a sad but common reality. One dishonest driver skimming off the top during loading or unloading, or siphoning fuel for later resale, can result in significant losses if undetected. This also applies to BOL discrepancies; whether intentional or accidental, BOL errors can result in deliveries being charged at the wrong rate or to the wrong destination.
Carrier error can add to fuel supply variance at this stage as well. Occasionally, an incorrect product is loaded into a trailer compartment or into a tank, or remnants retained on the trailer result in mixed or contaminated product. When the wrong product is delivered, a retailer receives inventory they did not order or intend to sell. If it can’t be easily resold, or if resources are needed to rectify the mistake, it can lead to a loss of revenue.
When fuel is delivered into a tank and reaches a critically high level, it can also cause spills, sprays, and equipment damage; overfill events like these bring about unplanned expense and downtime. In short, at the transport and delivery stage, fuel variance factors can turn any transaction into a headache of disputes and financial losses.
Other factors impacting fuel variance in the hauler phase include adjusted deliveries, a common issue that’s tough to measure. During fuel delivery at a high-volume, 24-hour location, for example, a retailer may have fuel dropping into their tank at the same time customers are pumping it out. The normal delivery process has no visibility into this, meaning that at the end of the delivery, they’re going to show a variance based on what they had on their truck versus what they physically dropped.
Likewise, fuel delivery can introduce inventory variance internally, on paper. Outdated billing systems often log incorrect delivery data, misstate numbers, cause tremendous lag time, and require extensive time and effort to reconcile records and invoices. Eventually, these discrepancies compound into larger more complex errors between what was delivered, what was billed, and what was actually in stock. It’s a scenario that not only erodes trust with suppliers but also complicates regulatory compliance and financial reporting.
Fuel stored in underground and above-ground tanks can be subject to variance factors even before being dispensed at the pump. Evaporation and meter drift–gradual changes in meter accuracy over time–and ATG calibration discrepancies can all contribute to inaccuracies between measured and actual fuel volumes. Seepage is another factor, with even minor leaks resulting in significant losses over time if left unchecked.
These seemingly minor inconsistencies can add up to significant losses, acting as a silent thief eating into profit margins. This is especially true for retailers who rely on traditional tank charts rather than fine grain tank chart technology which provides real-time, multi-point monitoring to quickly detect anomalies anywhere along the fuel supply chain. (We’ll discuss these more in our next post.)
Despite best practices, fuel theft is an endemic issue that’s timeless to the industry. It’s a worldwide problem as well, with theft costing approximately $133 billion USD per year globally.
While some may envision a heightened form of shoplifting, the reality is far more nefarious. Sophisticated theft rings have been known to use specialized devices to steal gas from pumps and resell it on the black market, or to physically change a pump’s pulser to alter the flow of fuel.
When traditional fuel retailers rely on paper-based systems and people resources, visibility is lost on an inventory management system comprised of many moving parts. This creates an optimal scenario for thieves seeking to commit fuel fraud.
Clearly, fuel inventory variance isn’t just a blip on the radar; it’s a systemic issue with far-reaching consequences. From financial losses to customer dissatisfaction, every point along the supply chain is vulnerable to its effects. And yet traditionally, variance throughout the fuel journey has been measured at limited checkpoints using various siloed methods.
In Part 2 of this series, we’ll dive into fine grain tank chart tracking capabilities and how this newer, more connected technology addresses variance issues from terminal to pump.