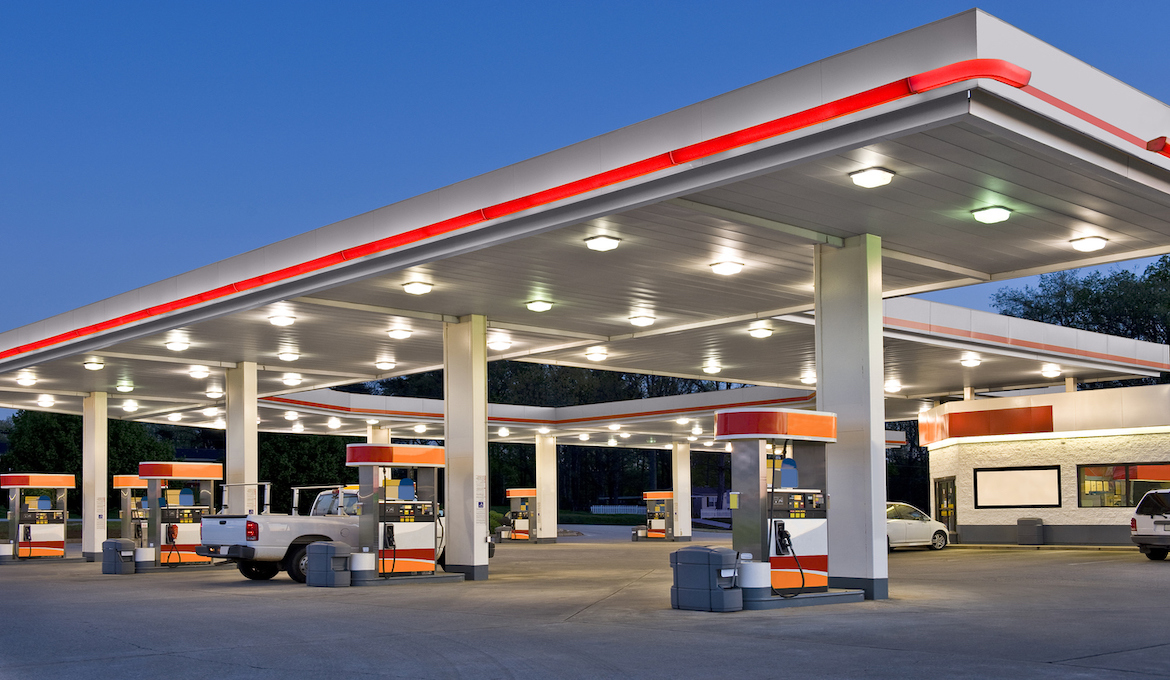
Webinar Recap: Fuel Inventory Variance Control – Why Speed and Precision Matter
In the first session of our latest webinar series, The Future of Filling Up: Faster, Easier, Frictionless, Titan Cloud’s Vice Presidents of Solutions Consulting Brent Puzak and Jeff Sexten discussed the most common issues affecting fuel customers, and how data-driven connectivity can greatly reduce pain at the pump.
Here are some takeaways from the conversation on frictionless fueling. To see a full recording of the Eliminating Pain Points at the Pump for Your Customers webinar, visit here.
In one webinar poll, most attendees reported that they routinely identify equipment issues in less than a day, or at most within five days. But resolving those issues takes much longer. Time to detect is one measurement, time to resolve is another; it’s that additional downtime that can frustrate customers at the pump who are faced with slow flow or a nozzle down.
Using the angry customer method is far too common in these scenarios. Fuel retailers often rely on a customer to arrive, find a bagged nozzle, or a slow flow dispenser, walk inside the store and complain to the clerks. Sexton recounted a recent experience in which his own frictionless fueling experience was impacted.
“Recently, I was one of those angered customers. I went to two different locations of the same brand, and both had over half their dispensers bagged out. I couldn’t wait, so I went to a different brand,” he said. “I’m a big brand loyalty person, and I went somewhere I never would have thought about going before. I had a good experience, the store was clean, I bought some things. That new brand just got a new customer because their dispensers were all up and running. It just grows from there.”
Titan Cloud research has found that reducing frequency and duration of system downtime can improve throughput by 3-4% with real-time visibility. By continuously processing data to detect anomalies minute to minute, fuel asset optimization technology can not only offer customers a frictionless fueling experience, but also provide notifications to retailers so they can address these issues significantly more quickly than waiting on that angry customer.
“As we’ve mentioned, there can be events where it takes a while for a customer to come into the store and actually report it. What we were seeing in the data is that average downtime is about six consecutive days of nozzle downtime,” Sexten said. “You have to think about how to reduce that duration. What would it look like if we could cut that down to three days, or two and a half? How would that lessen the burden on the customer and the loss of revenue?”
If customers are filling up faster, they’re happier. They also make room for more people to fill up at any given time. With an average customer transaction time of 15 minutes, the question becomes: Can a better flow rate lessen the time between transactions? Could it boost the volume of those transactions?
“At 15 minutes between these transactions, you’re getting four transactions an hour. Multiply that over your hours of operations. The question becomes, how can we get more transactions inside of that timeframe with a faster flow rate? Being able to have more data to analyze this over the course of time is going to provide you with better results,” Puzak said. “There’s value to having that visibility, to be able to act on that data to improve flow rate and total gallons to drive up revenue at your locations.”
Highlighting slow flow as a particularly prevalent pump frustration that prohibits frictionless fueling, Puzak and Sexton used the example of filter maintenance to demonstrate how early anomaly detection can make an immediate and tangible difference. While well over half of webinar attendees reported managing filter changes via reoccurring schedules, they learned that data analytics generated by fuel asset optimization technology can optimize those schedules to pinpoint which dispensers need attention.
“We know flow rate decreases over time without proper filter maintenance. Real-time monitoring provides data to identify precisely when the flow rate starts to drop off, and what filter needs to be changed so you’re not going out and changing all the filters at once if you don’t need it,” Puzak said. “Technology can also give you that visibility to know which ones are trending—that you may need to change out in the future—and if you’re sending a tech out there to fix something, you know exactly what fueling positions are down. That shortens your downtime because they’re not spending as much time on site trying to figure out what’s wrong.”
Hear the full Eliminating Pain Points at the Pump for Your Customers conversation here.
Fuel Inventory Variance Control: Why Speed and Precision Matter | April 24 | Register Here
From Chaos to Clarity: Demystifying Fuel Logistics | May 22 | Register Here