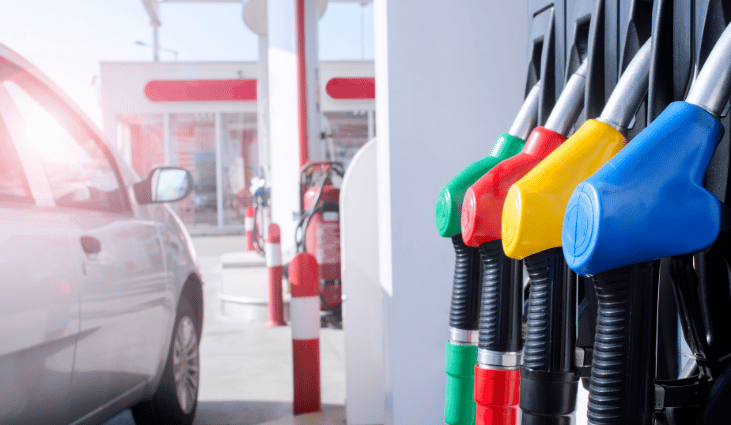
Fuel Inventory Variance Control: Speed & Precision Matter
In the second session of our Future of Filling Up: Faster, Easier, Frictionless webinar series, Titan Cloud’s Vice President of Solutions Consulting Brent Puzak and Solutions Consultant Michael Lewis discussed the negative chain reaction of undetected fuel inventory variance, and how real-time data analytics can help fuel operators get ahead of variance factors to mitigate loss. Below are some takeaways from the conversation.
To catch a full recording of the webinar, Fuel Inventory Variance Control: Why Speed and Precision Matter, visit here.
It’s a well-established fact that fuel inventory variance causes a domino effect of problems across the entire supply chain. Early detection and quick action are key to minimizing the damage, yet traditional systems still fall short when it comes to pinpointing the source of the problem.
“Most ERP systems have limited functionality when managing multiple concerns. They’re generating various reports, providing visibility that there’s loss, but they’re not able to identify the root cause of loss. If you can’t validate where that loss comes from, you can’t put steps in place to mitigate it. It’s decreasing the productivity of your teams,” Puzak said.
Part of the problem, he added, is that outdated tank charts can provide an incorrect baseline that throws off the entire tracking system from the start.
“The data that’s fed into these systems is coming from tank charts which have a lot of inaccuracies in them, and then from gauges which feed off the tank charts, so there are errors already baked in.”
Part of the problem with traditional tank charts is that they don’t consider physical imperfections, wear and tear over time, and other factors that can cause small errors in volume calculations. Those errors compile over time.
“These are the challenges that organizations face day in and day out, trying to reconcile a variance where you have these imperfections or deformities of the tank systems; they’re actually invoking additional variance points into the readings you’re capturing,” said Puzak. “A traditional tank chart with normal ATG programming is never going to catch that level of malformation within the structure.”
Lewis agreed, adding that tank imperfections can be inherent or can happen as the result of outside influences.
“Any sort of environmental factor, any sort of shift in the tank wear and tear over time, even if you’re in an area with frequent earthquake patterns,” he said. “Anything that’s going to disturb the relationship between the height and volume of your probe is a consideration.”
When fuel operators get a handle on what variances they have, and specifically which they can control, they’re able to focus operations teams on investigating actual issues instead of relying on guesswork.
“Many companies, no matter where they are around the world, are trying to investigate inventory loss with one arm tied behind their back. Leveraging new technology outside of what traditional ERP systems offer is like pulling off the blinders,” said Lewis. “A data-driven solution provides greater visibility and a much more granular view of what’s actually happening within your tanks and your tank systems. Whether it’s a tape leak or a meter calibration or stock probe—it can tidy out the noise within a variance audit on a day-by-day basis so you can have much more efficient workflows in fixing ongoing problems.”
Traditional tank charts rely on 4-20 monitoring points to extrapolate volume information. Even the higher end of that scale leaves plenty of room for inaccuracy when you consider tank imperfections, environmental factors, human error, and other impactful elements. Fine grain tank charts far surpass these capabilities, using 40,000 – 50,000 points of measurement for pinpoint granularity.
“A 20-point setup is going to give you more monitoring points and a shorter interpolation but at the end of the day, the challenge is still that you could have deviations between that are throwing off your overall readings,” said Lewis, explaining that fine grain tank chart technology uses tens of thousands of measurements to close that gap. “What we’re doing is we’re leveraging high- frequency data captured from inventory transactions on a continual basis. We’re counting for temperature, we’re counting for deliveries, any inputs and the outputs that are coming from the systems. This gives us a much more granular view than what you’re getting with a typical tank chart.”
To watch a recording of the full Fuel Inventory Variance Control: Why Speed and Precision Matter conversation, visit here.
From Chaos to Clarity: Demystifying Fuel Logistics | May 22 | Register Here