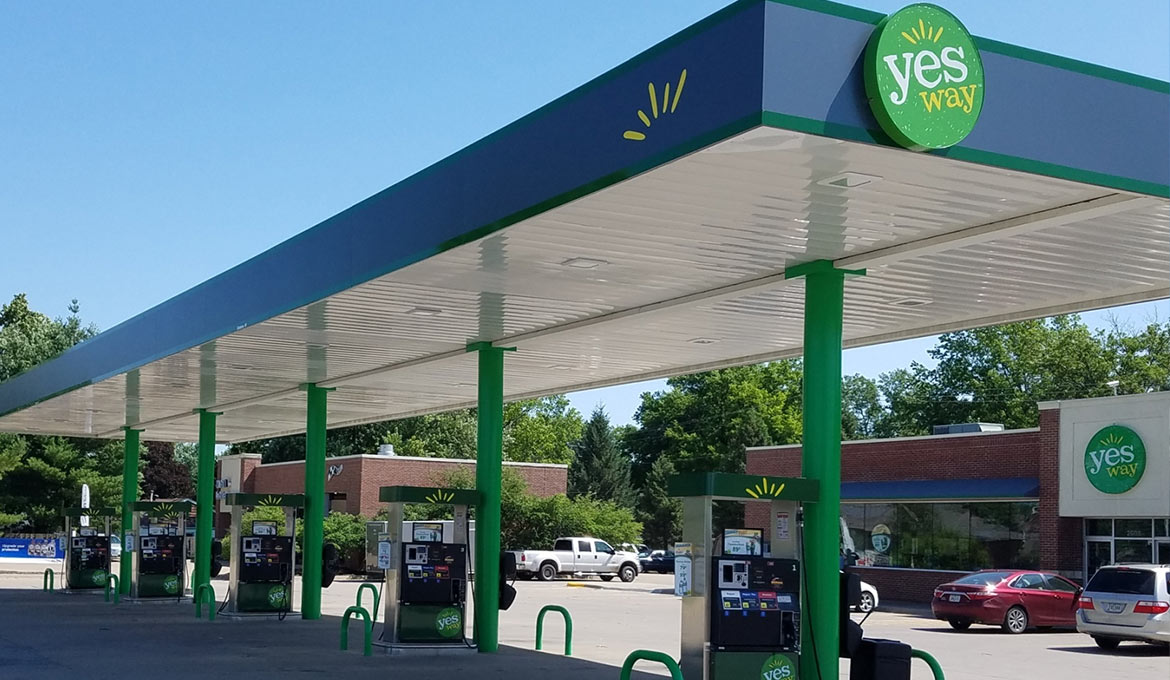
How Titan Cloud Helped Yesway Scale Its Compliance Program
As one of the largest wholesale distributors of fuel in New England and Upstate New York, Haffner’s (HAFFNER’S), which is owned by Energy North Incorporated (ENI), operates more than 70 gas stations, convenience stores, car washes, bulk fuel plants, home heating offices and foodservice locations. In addition to major brands, including Exxon, Mobil, Sunoco, Gulf and Citgo, HAFFNER’S is rapidly growing its Haffner’s and Tradewinds gas station and car wash brands and home heating business.
Much of its recent growth has derived from acquisitions, resulting in what had begun to feel like individual self-governing bodies, rather than one cohesive organization. HAFFNER’S needed to quickly unify a diverse, fragmented group of departments and management systems under one single source of truth to better manage its environmental compliance and L&P oversight for multiple areas (c-store and bulk plants).
“There are certain challenges that we expected with the rate of growth we have achieved,” said Melissa Davis, Senior Compliance Officer for Haffner’s. “Our teams need to efficiently share data across departments. This requires accurately assessing and reacting to that data, which ensures compliance across the business. Additionally, one of our core values is Do the Right Thing. It was very important to establish a compliance management system to help facilitate that core value from a compliance purview. Lastly, we needed to build a foundation for anticipated future growth.”
Navigating data, across a complicated and disjointed environment, placed a lot of stress on HAFFNER’S’s retail associates, who serve at the front line of the c-store business. Retail associates should focus on the customer experience. Compliance-related tasks should be centralized to remove added demands in a high-turnover area of the business and to place the burden on those trained specifically in the skill set and resources required to maintain compliance. These operations— which included environmental compliance and L&P documentation, automated tank gauge (ATG) alarm management, monthly release detection, 30-day walk-thru inspections, regulatory inspections, insurance requirements, testing, compliance-triggered R&M and more—functioned in silos using spreadsheets, manual data entry and vendor reliance, making it difficult to operate cohesively and efficiently. Compliance and L&P was primarily reactive rather than proactive.