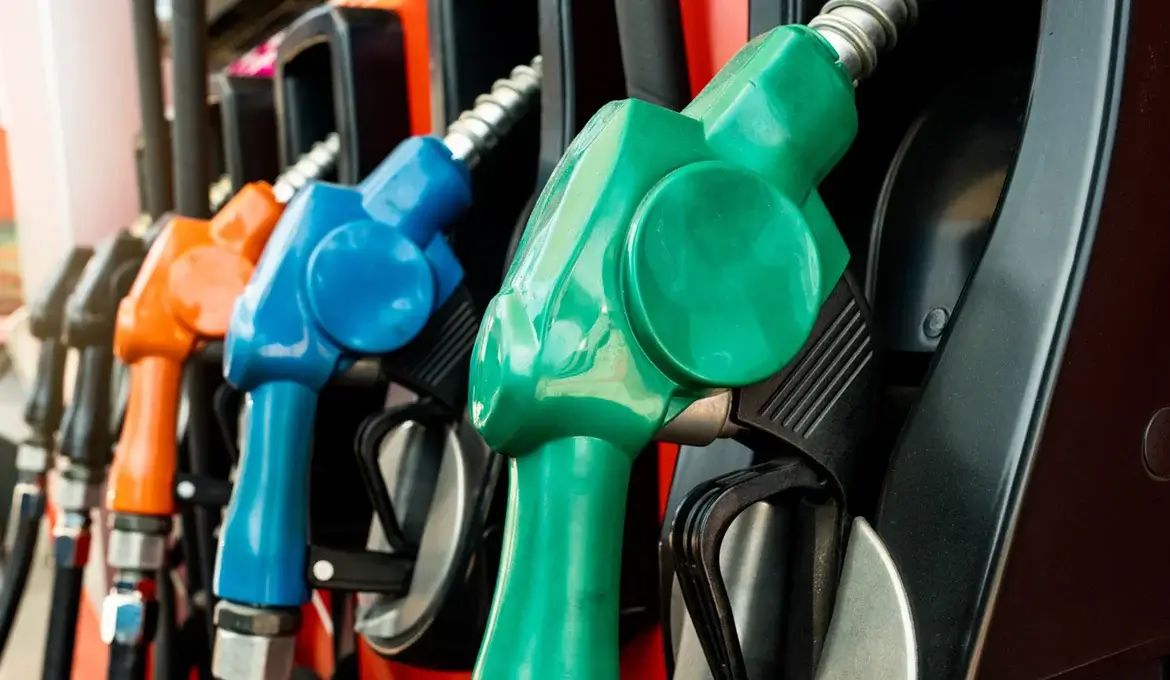
Real-Time Visibility into Fuel Theft and More
For retail fuel operators, ensuring a smooth and efficient customer experience at the pump is critical to maintaining a competitive edge. Even motorists who choose a service station based on price are likely to gauge their transaction from beginning to end before determining whether they become, or remain, a regular customer.
One influential factor in shaping this experience is flow rate—the speed at which fuel is dispensed from the nozzle to the vehicle. It may seem like a small pain point, but anyone who’s juggled a busy day knows how much extra stress a longer than anticipated gas stop can add. By the time the nozzle is out of the tank and back in the pump, a frustrated customer may decide not to return anytime soon.
In addition to the obvious influence on customer experience, flow rate issues can directly impact a retail fuel operator’s bottom line. In fact, as flow rate decreases, meter drift can increase, leading to measurement errors of 1% to 2%. As we’ve discussed in previous posts, a small differential across multiple pumps, stations and sites can add up to significant revenue loss for a company. Left undetected, low flow can trigger unnecessary recalibration, small leaks and compliance issues, and is essentially giving away fuel for free.
In most cases, low flow–and the inaccuracies it can trigger—are a result of issues that arise every day in the retail fuel industry. One such common culprit is clogged filters, something that if properly detected and addressed, can have less negative impact.
Fuel dispensers are typically calibrated to measure flow accurately within a certain range of flow rates. When filters become clogged, flow rate decreases, potentially dropping below the range where readings are most accurate. As a result, the dispenser may overestimate or underestimate the amount of fuel being dispensed. Other implications include:
Flow rate decreases over time without proper filter maintenance. But how can integrated technology detect such gradual loss in a way that enables retail fuel operators to fix the issue? To save otherwise lost inventory and revenue, it comes down to real-time monitoring and data analytics:
A comprehensive wetstock management or fuel management solution can help retail fuel operators minimize or eliminate flow-related issues. Titan Cloud’s software solution provides real-time data and predictive analytics, enabling operators to monitor tank levels, equipment status, and flow rates. To learn more, talk to one of our solutions consultants today.